Jindal Shadeed Iron & Steel

The Sultanate of Oman, under the wise and most admirable leadership of His Majesty Sultan Qaboos Bin Said has embraced steel as a bridge that continues to fast-track the nation’s incredible industrialisation and modernization drives in recent times
JINDAL SHADEED IRON & STEEL LLC.
The Sultanate of Oman, under the wise and most admirable leadership of His Majesty Sultan Qaboos Bin Said has embraced steel as a bridge that continues to fast-track the nation’s incredible industrialisation and modernization drives in recent times. Jindal Shadeed is an integral part of Jindal Steel and Power Limited (JSPL). Driven by excellence in innovation, under the dynamic leadership of honourable chairman Mr. Naveen Jindal, JSPL is one of India's major steel producers with a significant presence in sectors like Mining, Power Generation and Infrastructure. With an annual turnover of over US$ 3.5 billion, JSPL is a part of the US$ 18 billion diversified O. P. Jindal Group and is consistently tapping new opportunities by increasing production capacity, diversifying investments, and leveraging its core capabilities to venture into new businesses. Aligned with the vision of His Majesty to reduce country's dependency on Oil and Gas Sector – Jindal Shadeed is proud to be a key partner in this prestigious endeavourand committed to producing “Steel…that bridges your trust”. Jindal Shadeed has already made an investment of more than 1.1 billion USD. Jindal Shadeed, located strategically in the ancient port city of Sohar, is set over a 120-Hectare prime property, just 60-metres from the shoreline and adjacent to the busy Muscat-Dubai highway. Jindal Shadeed has an impressive line-up of facilities, geared to handle Oman’s growing need for Steel.Production Facilities:
Direct Reduced Iron (DRI) Plant
Our facilities include one Direct Reduction Plant supplied by Midrex Technologies USA, with a capacity of 1.5 MTPA of HBI (0.4 MTPA) and HDRI (1.1 MTPA). DR Plant has four briquetting machines for the production of hot briquetted iron (HBI) and is facilitated with the unique gravity feeding technology for transferring HDRI directly to Electric Arc Furnace of Steel melt shop. DR Plant mainly consists of Vertical shaft furnace, Reformer, Heat Recovery Unit, Seal gas system and Natural gas pre-treatment system. The spent gas which comes out of furnace and the flue gas from the Reformer are effectively re-used within the process and there is no wastage of gas from the process. It is very environmental friendly process and the emissions are well within the limits.Steel Melt Shop:
The plant consists of state-of-the-Art steel making facilities with the best features in terms of product range and productivity. The technological solution is characterized by the choice of high quality and productivity facilities by which it is possible to achieve extremely efficient operating results with low manpower and specific energy consumption, thereby making the plant highly competitive. SMS comprises of- 200t Electric Arc Furnace (EAF).
- 200t Ladle Refining Furnace (LF).
- 200 Ton Vacuum Degassing Unit (VD).
- Matching 8 strand Combi. Continuous Casting Machine to produce Square and round Billets/Blooms. The caster is first of its kind in the world.
Rolling Mill:
The latest addition to Jindal Shadeed’s array of innovative facilities is a prestigious 1.4 million tonne per annum Rolling Mill with advanced technology and equipment set up in collaboration with Danieli, Italy. The mill is capable of producing Rebars as per all International standards. Rolling Mill includes- Reheating Furnace.
- High Pressure Descaler.
- H-V combination Rolling Mill.
- Heat treatment equipment with QTB(Quenched & Tempered Bar) Technology
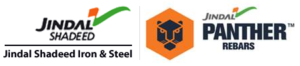